Introduction
In manufacturing, optimizing ergonomics and line balancing is crucial for productivity and worker well-being. Digital Manufacturing provides tools and techniques to enhance these aspects, ensuring efficient and safe operations. This blog explores the significance of ergonomic design and line balancing, highlighting the role of digital tools in achieving these goals.
Enhancing Ergonomics with Human Resource Simulation
The Importance of Ergonomics in Manufacturing Ergonomics is the science of designing workplaces and work tasks to fit the capabilities of the human body. In manufacturing, poor ergonomic design can lead to increased injury rates, decreased productivity, and higher absenteeism. Addressing ergonomic issues through proper design and simulation can lead to significant improvements in worker health, safety, and efficiency.
Human Resource Simulation Tools Human resource simulation tools use digital mannequins to replicate human tasks and interactions within a virtual environment. These tools assess various ergonomic factors such as posture, load, reachability, and visibility.
Key benefits include:
- Posture Analysis: By simulating different working postures, ergonomic tools help identify positions that minimize strain and discomfort, reducing the risk of musculoskeletal disorders.
- Load Assessment: These tools evaluate the physical load on workers during tasks, ensuring that weight limits are not exceeded and that lifting techniques are safe.
- Reachability and Accessibility: Ergonomic simulations analyze the reachability of tools, controls, and materials, ensuring that all necessary items are within easy reach, reducing unnecessary movements and strain.
- Visibility and Lighting: Ensuring that workers have clear visibility of their tasks and that workspaces are adequately lit enhances accuracy and reduces eye strain.
Improving Workplace Design By utilizing human resource simulation tools, manufacturers can design workstations that promote optimal ergonomics. This includes:
- Adjustable Workstations: Designing workstations that can be adjusted to fit different worker sizes and preferences.
- Proper Tool Placement: Ensuring that tools and materials are placed within easy reach to minimize awkward postures and movements.
- Supportive Equipment: Incorporating supportive equipment like ergonomic chairs and lifting aids to reduce physical strain.
Effective Line Balancing Techniques
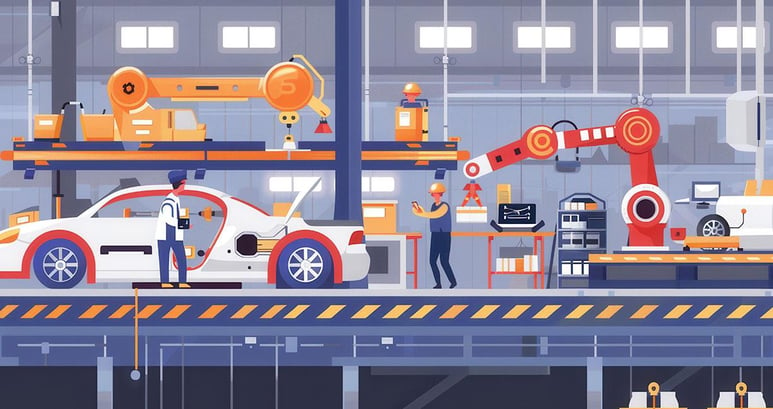
The Role of Line Balancing in Manufacturing Line balancing involves distributing tasks evenly across all workstations in a production line to ensure smooth and efficient operations. An unbalanced line can lead to bottlenecks, idle time, and reduced productivity. Effective line balancing is essential for maintaining high production rates and minimizing downtime.
Computer-Aided Tools for Line Balancing Digital Manufacturing tools for line balancing use advanced algorithms and simulation models to optimize the distribution of tasks across workstations. These tools consider various factors such as task duration, operator skills, and equipment capabilities.
Key benefits include:
- Optimizing Workload Distribution: By analysing task durations and dependencies, line balancing tools ensure that each workstation has a balanced workload, preventing bottlenecks and idle time.
- Adjusting to Production Fluctuations: These tools can quickly adapt to changes in production volumes, ensuring that the line remains balanced even as demand fluctuates.
- Considering Operator Skills: Line balancing tools take into account the skills and capabilities of individual operators, ensuring that tasks are assigned to the most suitable workers.
Manual vs. Computer-Aided Line Balancing While manual line balancing relies on time studies and operator feedback, computer-aided tools provide a more comprehensive and accurate approach. Manual methods often fail to consider all underlying constraints, such as activity grouping, operator skill levels, and resource limitations. Digital tools, on the other hand, can evaluate multiple scenarios quickly and accurately, ensuring optimal results.
Case Studies and Real-World Examples Real-world applications of ergonomic and line balancing simulations demonstrate significant improvements in productivity and operator well-being. Here are a few examples:
- Automotive Manufacturing: In an automotive assembly plant, ergonomic simulations helped redesign workstations to reduce worker strain. By optimizing tool placement and workstation height, the plant saw a reduction in musculoskeletal injuries and an increase in productivity.
- Electronics Manufacturing: A manufacturer of electronic devices used line balancing tools to optimize their production line. By analysing task durations and dependencies, they were able to eliminate bottlenecks and improve throughput, reducing production time by 15%.
- Aerospace Manufacturing: An aerospace manufacturer used human resource simulation tools to design ergonomic workstations for aircraft assembly. This resulted in improved worker comfort and a 20% reduction in assembly errors, enhancing overall product quality.
Conclusion
Optimizing ergonomics and line balancing through Digital Manufacturing tools leads to safer, more productive manufacturing environments. By leveraging advanced simulation tools, manufacturers can design workstations that minimize worker strain, distribute tasks evenly across production lines, and adapt to changing production demands.
Digital tools for ergonomic design and line balancing not only improve worker health and safety but also enhance overall efficiency and productivity. As these technologies advance, their benefits will continue to grow, driving further improvements in manufacturing processes and worker satisfaction.
For an in-depth understanding of how digital manufacturing optimizes ergonomics and line balancing, visit our service page.