Attention
This website is best viewed in portrait mode.
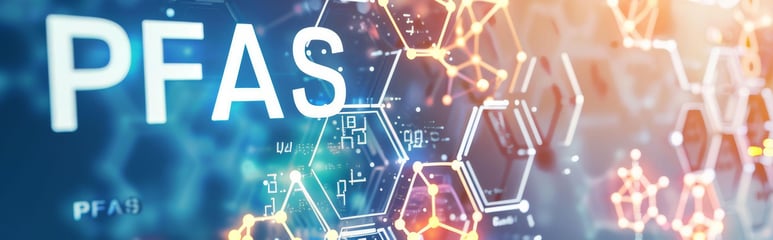
Navigation
Navigation- Introduction
- What are PFAS?
- Overview of PFAS Regulations
- Key Regulatory Authorities and Their Roles
- Impact of PFAS Regulations on Medical Device Manufacturers
- Strategies for Achieving PFAS Compliance
- Common Challenges in PFAS Regulatory Compliance
- Best Practices for Navigating PFAS Regulations
- FAQs: Common Questions Answered about PFAS Compliance for Medical Devices
- Conclusion
- Partner with Tata Elxsi for Expert PFAS Compliance Solutions
Introduction
Per- and polyfluoroalkyl substances (PFAS) are a group of man-made chemicals widely used in various industrial applications, including the manufacturing of medical devices. Due to their persistence in the environment and potential health risks, PFAS are under increased regulatory scrutiny. This comprehensive guide aims to help medical device manufacturers understand and navigate the complex landscape of PFAS regulations, ensuring compliance while maintaining innovation and quality.
What are PFAS?
Per- and polyfluoroalkyl substances (PFAS) are a large class of thousands of synthetic chemicals that are used throughout society.
They all contain C-F bonds, which are one of the strongest chemical bonds in organic chemistry. This means that they resist degradation when used. Most PFAS are also easily transported in the environment covering long distances away from the source of their release.
They are known for their resistance to heat, water, and oil, which makes them valuable in numerous applications such as non-stick cookware, firefighting foams, and, notably, medical devices. However, their environmental persistence and potential adverse health effects have led to growing concerns and regulatory actions worldwide.
Overview of PFAS Regulations
Regulations surrounding PFAS are rapidly evolving, with various countries and regions introducing laws and guidelines to control the use and emissions of PFAS across the globe. For medical device manufacturers, understanding these regulations is crucial to ensure compliance and avoid potential penalties.
In the United States, the Environmental Protection Agency (EPA) has been proactive in setting guidelines for PFAS levels in drinking water and industrial discharges. The European Chemicals Agency (ECHA) has implemented restrictions under the REACH regulation, while other countries like Canada, Australia, and Japan have introduced their own sets of rules.
1. Global Regulatory Landscape
a. International Treaties and Agreements
- Stockholm Convention on Persistent Organic Pollutants: The Stockholm Convention, an international treaty aimed at eliminating or restricting the production and use of persistent organic pollutants (POPs), includes PFOS and PFOA in its annexes. The convention's restrictions focus on limiting the use of these substances due to their harmful environmental and health effects (UNEP).
- OECD Guidelines: The Organization for Economic Co-operation and Development (OECD) provides guidelines for the assessment and management of PFAS chemicals. The OECD’s PFAS strategy emphasizes the need for member countries to develop and implement regulatory measures to manage PFAS risks (OECD).
b. Global Initiatives
- Global PFAS Assessment: Several global initiatives, including those led by the United Nations Environment Programme (UNEP), work to assess the global impact of PFAS and promote international regulatory cooperation. These initiatives aim to harmonize regulations and share best practices across borders (UNEP).
2. European Union Regulations
a. REACH Regulation
- Overview: The European Union’s REACH (Registration, Evaluation, Authorization, and Restriction of Chemicals) regulation is one of the most comprehensive frameworks for managing chemical substances. Under REACH, PFAS are subject to registration, and certain PFAS substances are restricted or banned (ECHA).
- Specific Restrictions: Recent amendments to REACH include restrictions on the use of specific PFAS substances in consumer products and industrial applications. The European Chemicals Agency (ECHA) has proposed restrictions on the use of PFAS in articles, and is pushing for PFAS-free medical devices, due to their persistence and potential health impacts (ECHA).
b. Medical Device Regulation (MDR)
- Overview: The EU Medical Device Regulation (MDR) governs the safety and performance of medical devices within the EU. While the MDR itself does not specifically address PFAS, manufacturers must comply with all relevant chemical regulations, including REACH, when placing devices on the market (European Commission).
- Implications for PFAS: Manufacturers must ensure that their devices do not contain restricted PFAS substances and that they meet all regulatory requirements related to chemical safety and material composition (ECHA).
3. United States Regulations
a. Environmental Protection Agency (EPA)
- PFAS Action Plan: The U.S. Environmental Protection Agency (EPA) has developed a PFAS Action Plan that outlines strategies for managing PFAS risks, including regulatory actions to limit PFAS in drinking water and other environmental media (EPA).
- Specific Regulations: The EPA has proposed regulations under the Safe Drinking Water Act (SDWA) to set limits on PFAS in drinking water. Although these regulations focus primarily on environmental media, they also impact industries, including medical device manufacturers, through regulatory compliance requirements (EPA).
b. State-Level Regulations
- Varied Approaches: In addition to federal regulations, several U.S. states have enacted their own PFAS regulations. For example, California has implemented strict regulations on PFAS in various consumer products, including medical devices. States like New York and Michigan have also introduced legislation targeting PFAS (California Department of Public Health).
- Implications for Manufacturers: Manufacturers must stay informed about state-level regulations and ensure compliance with both federal and state requirements. This may involve adapting processes, conducting additional testing, and maintaining up-to-date documentation (NCSL).
4. Asia-Pacific Regulations
a. China’s REACH-Like Regulation
- Overview: China has implemented its own chemical regulation framework, similar to REACH, which includes provisions for managing hazardous chemicals like PFAS. The regulation focuses on chemical registration and risk management (MEE).
- Implications for Medical Devices: Manufacturers exporting medical devices to China must ensure compliance with local regulations regarding PFAS and other hazardous substances. This may require additional testing and certification (China National Chemical Information Center).
b. Japan’s Chemical Substances Control Law
- Overview: Japan’s Chemical Substances Control Law regulates the manufacture, import, and use of chemical substances, including PFAS. The law aims to manage chemical risks and ensure safety in consumer products (J-CHECK).
- Implications for Medical Devices: Medical device manufacturers must comply with Japanese regulations on PFAS and other chemicals, which includes meeting safety standards and providing appropriate documentation (Japan Ministry of the Environment).
Key Regulatory Authorities and Their Roles
EPA (Environmental Protection Agency, USA): The EPA sets guidelines and regulations for PFAS levels in drinking water and industrial discharges. In 2020, the EPA proposed a rule to require reporting on PFAS manufacture and import, signaling increased scrutiny.
ECHA (European Chemicals Agency): Under the REACH regulation, ECHA has listed several PFAS substances as substances of very high concern (SVHC), requiring authorization for use.
Other International Bodies: Similar regulatory efforts are underway in countries like Canada, Australia, and Japan, each adapting their approach based on local environmental and public health priorities.
Impact of PFAS Regulations on Medical Device Manufacturers
PFAS regulations are transforming the landscape for medical device manufacturers. As regulatory bodies impose stricter standards on the use of per- and polyfluoroalkyl substances (PFAS), manufacturers must navigate a complex array of compliance requirements. The impact of these regulations extends across various dimensions, including monetary costs, operational adjustments, and market dynamics.
1. Monetary Impact
The financial ramifications of PFAS regulations are substantial. Here are some key areas where monetary impacts are observed:
Compliance Costs: Adhering to PFAS regulations often requires significant investments. Costs may include the following:
- Material Substitution: Replacing PFAS-containing materials with compliant alternatives can be costly. According to Chemical & Engineering News, transitioning from PFAS-coated components to PFAS-free substitutes can increase material costs by up to 20% (Chemical & Engineering News).
- Process Reengineering: Adjusting manufacturing processes to eliminate PFAS or reduce its concentration involves expenses related to equipment upgrades, process validation, and quality control. These adjustments can add tens of thousands of dollars to a company’s operational budget. For instance, process modifications in the semiconductor industry, which face similar regulatory pressures, have been reported to cost between $50,000 and $200,000 per modification (Journal of Cleaner Production).
- Testing and Certification: Ongoing testing and certification to ensure PFAS compliance can also be expensive. depending on the complexity and frequency of testing (Environmental Science & Technology).
- Fines and Penalties: Non-compliance with PFAS regulations can result in substantial fines and penalties. Recent enforcement actions by the EPA have led to fines ranging from $50,000 to $2 million for companies failing to meet PFAS standards (EPA Enforcement Reports). Additionally, companies may face costly legal battles and settlements, with legal costs averaging between $100,000 and $500,000 per case in environmental disputes (Environmental Law Reporter).
- Market Access Costs: Complying with PFAS regulations may affect market access, especially for international markets with varying regulations. The cost of obtaining certifications and meeting international standards can be significant.
2. Operational Impact
PFAS regulations necessitate several operational changes within medical device manufacturing:
- Supply Chain Adjustments: Manufacturers must work closely with suppliers to ensure that all materials and components meet PFAS compliance standards. This involves auditing suppliers, negotiating new contracts, and sometimes sourcing from alternative suppliers, which can disrupt established supply chains and lead to increased procurement costs. In the automotive industry, similar supply chain adjustments have been reported to increase costs by approximately 10% (Automotive News).
- Process Changes: Manufacturers may need to re-engineer production processes to eliminate PFAS. This includes investing in new technologies, modifying production lines, and training staff to handle new materials or procedures. The transition period can lead to temporary production delays and inefficiencies. For instance, re-engineering processes in the electronics industry has been shown to cause production delays of up to 6 months (IEEE Spectrum).
- Documentation and Reporting: Enhanced regulatory scrutiny requires meticulous documentation and reporting. Manufacturers must maintain detailed records of PFAS testing, compliance measures, and certification processes. Implementing robust documentation systems can increase administrative burdens and require additional resources, with some organizations reporting up to a 15% increase in administrative costs due to enhanced reporting requirements (Journal of Environmental Management).
3. Market Dynamics
PFAS regulations can influence market dynamics in several ways:
- Competitive Advantage: Companies that proactively address PFAS regulations may gain a competitive advantage by demonstrating their commitment to safety and sustainability. This can enhance brand reputation and attract customers who prioritize compliance and environmental responsibility. A survey by Environmental Leader found that 72% of consumers prefer products from companies with strong sustainability practices (Environmental Leader).
- Product Innovation: Regulations often drive innovation as manufacturers seek to develop new materials and technologies that meet compliance requirements. Investing in research and development to create PFAS-free alternatives can lead to innovative products and open new market opportunities. In the tech industry, companies investing in sustainable innovation have seen revenue increases of up to 30% (McKinsey & Company).
- Consumer Trust: Compliance with PFAS regulations can bolster consumer trust. As awareness of PFAS-related health risks grows, consumers are increasingly looking for products from companies that prioritize regulatory compliance and environmental stewardship. This can positively impact sales and brand loyalty. A report by Nielsen found that 66% of global consumers are willing to pay more for sustainable products (Nielsen).
4. Long-Term Strategic Impact
- Regulatory Trends: The evolving regulatory landscape suggests that PFAS restrictions may become more stringent over time. Companies that invest in PFAS reduction strategies early can better position themselves for future regulatory changes and avoid the higher costs associated with last-minute compliance efforts.
- Sustainability Goals: Embracing PFAS reduction aligns with broader sustainability goals and corporate social responsibility (CSR) initiatives. By reducing PFAS use, companies can contribute to environmental protection and enhance their CSR profiles, which can be advantageous in attracting investors and stakeholders.
Strategies for Achieving PFAS Compliance
Achieving PFAS compliance is a complex process requiring a multifaceted approach. Medical device manufacturers must navigate a web of regulations and industry standards to ensure their products meet the stringent requirements related to PFAS (per- and polyfluoroalkyl substances). Here, we explore key strategies for achieving PFAS compliance, including risk assessment, material substitution, process optimization, and ongoing monitoring.
1. Risk Assessment and Management
a. Comprehensive Risk Assessment
The first step in achieving PFAS compliance is conducting a thorough risk assessment. This involves identifying potential sources of PFAS in the manufacturing process and assessing the risk associated with each source. This can include:
- Materials Review: Evaluate all raw materials, components, and finished products for PFAS content. Use advanced analytical methods such as mass spectrometry to detect PFAS levels with high accuracy (Environmental Science & Technology).
- Process Evaluation: Assess manufacturing processes to determine where PFAS might be introduced. This includes examining process chemicals, coatings, and other additives.
- Supply Chain Analysis: Work with suppliers to identify and mitigate PFAS risks in the supply chain. Supplier audits and certifications can help ensure that components meet PFAS-free standards.
b. Risk Mitigation Strategies
Once risks are identified, develop and implement strategies to mitigate them. This can include:
- Substitute Materials: Replace PFAS-containing materials with safer alternatives. For example, use fluorine-free coatings and adhesives that do not contain PFAS (Journal of Cleaner Production).
- Process Improvements: Modify manufacturing processes to eliminate the use of PFAS-containing substances. This might involve re-engineering processes or investing in new technologies.
- Training and Awareness: Educate staff about PFAS risks and compliance requirements. Implement training programs to ensure that employees understand their roles in managing PFAS-related issues.
2. Material Substitution
a. Identifying Alternatives
Finding and implementing PFAS-free alternatives is a crucial aspect of compliance. Here’s how to approach material substitution:
- Research and Development: Invest in R&D to identify and develop PFAS-free materials. Collaborate with material scientists and suppliers to explore new, compliant materials (Materials Today).
- Case Studies: Learn from industry case studies where successful PFAS substitutions have been made. For example, the automotive industry has successfully transitioned to PFAS-free materials in various applications (Automotive News).
b. Testing and Validation
Once alternatives are identified, conduct rigorous testing and validation to ensure that they meet performance and safety standards:
- Performance Testing: Ensure that new materials perform as well as or better than the PFAS-containing ones in terms of durability, safety, and efficacy.
- Regulatory Compliance: Verify that substituted materials meet all regulatory requirements for PFAS content and other relevant standards.
3. Process Optimization
a. Process Engineering
Optimize manufacturing processes to minimize or eliminate PFAS use:
- Technology Upgrades: Invest in advanced manufacturing technologies that do not rely on PFAS. For instance, use alternative coating technologies that do not involve PFAS (IEEE Spectrum).
- Process Control: Implement process controls to monitor and manage PFAS levels. Utilize real-time monitoring systems to ensure compliance throughout the production cycle (Journal of Environmental Management).
b. Continuous Improvement
Adopt a continuous improvement approach to refine processes and ensure ongoing compliance:
- Regular Audits: Conduct regular internal and external audits to assess PFAS compliance. Identify areas for improvement and address any non-compliance issues promptly.
- Feedback Mechanisms: Establish feedback mechanisms to collect and analyze data on PFAS management. Use this data to drive process improvements and enhance compliance strategies.
4. Ongoing Monitoring and Reporting
a. Monitoring Systems
Implement robust monitoring systems to track PFAS levels and ensure ongoing compliance:
- Environmental Monitoring: Monitor environmental conditions in manufacturing facilities to detect any PFAS emissions or contamination (EPA Environmental Reports).
- Product Testing: Regularly test products for PFAS content to ensure that they meet compliance standards throughout their lifecycle.
b. Reporting and Documentation
Maintain comprehensive documentation and reporting to demonstrate compliance:
- Compliance Records: Keep detailed records of PFAS testing, material substitutions, and process changes. This documentation is crucial for regulatory audits and inspections (ISO Certification).
- Regulatory Updates: Stay informed about changes in PFAS regulations and update compliance strategies accordingly. Subscribe to industry newsletters and regulatory updates to remain current on new requirements.
5. Engagement with Regulatory Bodies
a. Regulatory Liaison
Engage with regulatory bodies to stay informed and ensure compliance:
- Consultations: Consult with regulatory agencies to clarify compliance requirements and seek guidance on complex issues.
- Participation in Industry Groups: Join industry groups and forums focused on PFAS regulations. Participate in discussions and collaborate with peers to share best practices and stay updated on regulatory changes (FDA Guidelines).
b. Advocacy
Advocate for clear and practical regulations:
- Feedback: Provide feedback to regulatory bodies on proposed PFAS regulations. Advocate for clear and feasible compliance requirements that support innovation while protecting public health.
- Collaboration: Collaborate with industry associations and regulatory agencies to develop and refine PFAS compliance guidelines.
Common Challenges in PFAS Regulatory Compliance
Achieving PFAS compliance presents a range of challenges for medical device manufacturers. These challenges stem from the complex nature of PFAS regulations, the inherent properties of PFAS compounds, and the practical difficulties in adapting manufacturing processes and materials. This section delves into some of the most common challenges faced by manufacturers and offers insights into how they can be effectively addressed.
1. Complexity of PFAS Regulations
a. Fragmented Regulatory Landscape
One of the primary challenges is navigating the fragmented regulatory landscape for PFAS:
- Varied Standards: PFAS regulations can differ significantly across countries and regions. For instance, while the European Union has established stringent PFAS limits under REACH (Registration, Evaluation, Authorization and Restriction of Chemicals), the U.S. Environmental Protection Agency (EPA) has its own set of guidelines that may vary (ECHA). This variation can create confusion and complicate compliance for manufacturers operating in multiple markets.
- Evolving Guidelines: Regulations are frequently updated as new scientific information emerges. Staying current with these changes and ensuring ongoing compliance can be challenging. For example, recent updates to the PFAS regulatory framework in the U.S. have introduced stricter limits and additional reporting requirements (EPA).
b. Interpretation of Regulations
Interpreting and applying PFAS regulations to specific manufacturing processes and products can be difficult:
- Ambiguity in Definitions: Regulatory definitions of PFAS and their acceptable limits may be ambiguous, leading to uncertainty about compliance requirements. For example, some regulations define PFAS broadly, while others have specific lists of regulated substances (Environmental Science & Technology).
- Guidance Interpretation: Manufacturers often face challenges in interpreting regulatory guidance and implementing it effectively. The need for expert legal and regulatory advice can add to compliance costs (Harvard Law School).
2. Identification and Testing of PFAS
a. Detection Difficulties
Detecting PFAS in materials and products can be challenging due to the following factors:
- Chemical Complexity: PFAS compounds are a large and diverse group of substances with varying chemical structures. Detecting all forms of PFAS, especially those in low concentrations, requires advanced analytical techniques (American Chemical Society).
- Testing Costs: High-quality PFAS testing, and analysis can be expensive. The cost of using sophisticated Analytical techniques and specialized laboratories can range from $5,000 to $15,000 per test, which may be expensive for smaller manufacturers (EPA).
b. Sampling and Validation
Accurate sampling and validation are critical to ensure compliance:
- Sample Collection: Collecting representative samples for testing can be difficult, especially if PFAS contamination is unevenly distributed. Proper sampling techniques are essential to obtain accurate results (Journal of Environmental Management).
- Validation Challenges: Validating testing methods and ensuring their reliability over time can be complex. Manufacturers must invest in ongoing validation efforts to maintain accuracy (ISO).
3. Material Substitution and Process Changes
a. Finding Alternatives
Identifying and implementing PFAS-free alternatives can be a significant challenge:
- Limited Alternatives: Suitable PFAS-free alternatives may not always be available or may not meet the performance requirements of existing materials. For example, finding alternatives to PFAS-based coatings with equivalent durability can be challenging (Materials Today).
- Performance Issues: Newly identified alternatives may not perform as well as PFAS-containing materials, which can impact product quality and safety. Manufacturers need to balance regulatory compliance with product performance (Chemical & Engineering News).
b. Process Adaptations
Modifying manufacturing processes to accommodate PFAS-free materials can be difficult:
- Equipment Compatibility: Existing manufacturing equipment may not be compatible with new materials or processes. Adapting or replacing equipment can be costly and time-consuming (IEEE Spectrum).
- Training Needs: Staff training is required to handle new materials and processes safely and effectively. This training can involve additional costs and operational downtime (Journal of Cleaner Production).
4. Cost of Compliance
a. Direct Costs
Compliance with PFAS regulations incurs several direct costs:
- Testing and Certification: Ongoing costs for PFAS testing, certification, and documentation can be significant. For instance, obtaining and maintaining certifications for PFAS-free products can range from $10,000 to $50,000 depending on the complexity of the certification process (ISO Certification).
- Process Changes: Investing in new technologies and process improvements to eliminate PFAS can be expensive. Manufacturers may need to allocate substantial budgets for equipment upgrades and process reengineering (EPA Enforcement Reports).
b. Indirect Costs
Compliance can also lead to indirect costs:
- Operational Disruptions: Changes to manufacturing processes and materials can lead to temporary production disruptions and decreased efficiency. Manufacturers may experience delays and increased operational costs during the transition period (Journal of Environmental Management).
- Market Access Costs: Meeting international PFAS regulations may require additional certifications and documentation, increasing the cost of accessing global markets (Automotive News).
5. Keeping Up with Evolving Regulations
a. Regulatory Updates
- Frequent Changes: Regulations are continually updated as new research and data become available. Keeping up with these changes requires dedicated resources and expertise
- Global Variations: Manufacturers operating internationally must comply with varying regulations in different jurisdictions, adding to the complexity of regulatory management (ECHA).
b. Resource Allocation
Allocating resources to manage regulatory compliance can be challenging:
- Staffing Needs: Ensuring that regulatory compliance teams are adequately staffed and trained is essential but can be resource intensive. Organizations may need to invest in specialized personnel or consultants (Harvard Law School).
- Financial Planning: Developing and implementing a financial plan to cover compliance costs and manage potential financial impacts is crucial for long-term sustainability (McKinsey & Company).
Best Practices for Navigating PFAS Regulations
Implementing best practices can help medical device manufacturers navigate the complex regulatory landscape:
- Employee Training: Educate your employees about PFAS regulations and their implications. Ensure they understand the importance of compliance and the steps necessary to achieve it.
- Supply chain transparency & Risk Assessment: Work closely with suppliers to understand the presence of PFAS in raw materials and components and implement stringent supplier audits & require disclosure of PFAS content along with Conducting risk assessments of company products and Supply chain to evaluate the potential impact of PFAS on product safety, efficacy, and regulatory compliance. Implement mitigation strategies based on the assessment results.
- Engage with Regulators: Maintain open communication with regulatory bodies. Participate in public consultations and industry working groups to stay informed about upcoming regulations and provide feedback. Monitoring both regulatory evolution and developing litigation related to PFAS.
- Proactive Testing: Ensuring raw materials are tested for PFAS presence & quantification. Testing finished products to confirm the absence of PFAS or confirming the use of PFAS-containing materials is within the specifications for your products.
- Conduct Regular Audits: Regularly review products and supply chains for PFAS compliance. This includes conducting internal audits and third-party inspections.
- Invest in R&D: Allocate resources to research and development to identify and test alternatives to PFAS. Collaboration with universities and research institutions can accelerate innovation. Prepare the R&D plan for substitution of PFAS materials considering the derogation period.
- Customer communication: Be transparent with customers about the presence of PFAS in your products and your efforts to comply with regulations.
- Regulatory Strategy: Define new product regulatory strategy as per updated regulations (including rationales, biocompatibility reports, feasibility reports, lab testing reports, design change reports etc. as per applicability)
FAQs: Common Questions Answered about PFAS Compliance for Medical Devices
Understanding PFAS (per- and polyfluoroalkyl substances) compliance can be complex for medical device manufacturers. This section addresses common questions and concerns regarding PFAS compliance to provide clarity and support in navigating the regulatory landscape.
1. What are PFAS and why are they regulated?
a. Definition and Characteristics
Per- and polyfluoroalkyl substances (PFAS) are a large class of thousands of synthetic chemicals that are used throughout society.
They all contain C-F bonds, which are one of the strongest chemical bonds in organic chemistry. This means that they resist degradation when used and also in the environment. Most PFAS are also easily transported in the environment covering long distances away from the source of their release.
b. Regulation Rationale
PFAS are regulated primarily due to their environmental persistence and potential health risks. Studies have linked PFAS exposure to various health issues, including cancer, liver damage, and developmental effects (CDC). Regulatory bodies aim to limit exposure to these chemicals to protect public health and the environment.
2. What are the key regulations regarding PFAS for medical devices?
a. Major Regulations
Key regulations for PFAS in medical devices include:
- EU REACH Regulation: The European Union’s REACH regulation restricts the use of certain PFAS substances and requires manufacturers to demonstrate that their products do not contain restricted PFAS (ECHA).
- State-Level Regulations: In the U.S., several states have enacted their own PFAS regulations, which can vary significantly from federal guidelines. For example, California has its own set of restrictions for PFAS in consumer products (California Department of Public Health).
b. Industry Standards
In addition to regulations, industry standards such as ISO 13485 (Medical devices – Quality management systems) may require compliance with safe materials.
3. How can manufacturers determine if their products contain PFAS?
a. Testing and Analysis
Determining PFAS content involves specialized testing:
- Analytical Techniques: High-performance liquid chromatography coupled with tandem mass spectrometry (LC-MS/MS) is commonly used for detecting PFAS in materials and products. This method can identify and quantify various PFAS compounds at very low concentrations (American Chemical Society).
- Third-Party Labs: Manufacturers may need to partner with accredited third-party laboratories specializing in PFAS analysis. These labs can provide comprehensive testing services to ensure that products meet regulatory standards (EPA).
b. Supply Chain Transparency
Ensuring that suppliers provide information on the PFAS content of their materials is crucial. This may involve requesting detailed Material Safety Data Sheets (MSDS) and certifications from suppliers (ISO Certification).
4. What are the best practices for achieving PFAS compliance?
a. Material Substitution
Switching to PFAS-free materials is one of the most effective ways to ensure compliance:
- Research Alternatives: Invest in research to identify and test alternative materials that do not contain PFAS. Collaborate with suppliers and industry experts to find suitable replacements (Journal of Cleaner Production).
- Certification and Validation: Ensure that alternative materials meet regulatory requirements and perform as expected in the final product. Validate materials through rigorous testing and certification (Materials Today).
b. Process Optimization
Optimize manufacturing processes to minimize PFAS use:
- Process Changes: Modify processes to eliminate the need for PFAS-containing substances. Invest in new technologies and equipment that support PFAS-free manufacturing (IEEE Spectrum).
- Training and Awareness: Train staff on PFAS regulations and compliance requirements. Foster a culture of compliance through regular training and updates (Journal of Environmental Management).
5. How can manufacturers prepare for potential PFAS bans?
a. Strategic Planning
Preparing for a PFAS ban involves strategic planning and proactive measures:
- Scenario Analysis: Conduct scenario analyses to understand the potential impact of a PFAS ban on your products and operations. Identify key areas where PFAS are used and develop alternative strategies (McKinsey & Company).
- Regulatory Monitoring: Stay informed about potential regulatory changes and prepare to adapt to new requirements. Monitor updates from regulatory bodies and industry associations (EPA).
b. Engagement and Advocacy
Engage with regulators and industry groups to influence and understand upcoming regulations:
- Regulatory Engagement: Participate in regulatory consultations and provide feedback on proposed PFAS bans. Collaborate with industry groups to advocate for practical and feasible regulations (Harvard Law School).
- Industry Collaboration: Work with other manufacturers and industry associations to share best practices and strategies for managing PFAS-related challenges (FDA Guidelines).
6. What resources are available for manufacturers seeking to understand PFAS regulations?
a. Regulatory Agencies
Several regulatory agencies provide valuable resources:
- Environmental Protection Agency (EPA): Offers guidance documents, compliance assistance, and updates on PFAS regulations (EPA).
- European Chemicals Agency (ECHA): Provides information on PFAS regulations under REACH and other relevant directives (ECHA). RAC & SEAC
b. Industry Associations
Industry associations often offer resources, including:
- Medical Device Manufacturers Associations: Many associations provide guidance documents, webinars, and best practice guidelines on PFAS compliance (FDA).
- Consulting Firms: Specialized consulting firms offer expert advice on regulatory compliance, testing, and material substitution
Conclusion
Navigating the Complex World of PFAS Regulations
As the regulatory landscape surrounding PFAS (per- and polyfluoroalkyl substances) becomes increasingly complex, medical device manufacturers face significant challenges and opportunities. Understanding and complying with PFAS regulations is critical for ensuring the safety of medical devices and mitigating potential risks associated with these persistent chemicals.
The challenges associated with PFAS regulatory compliance are multifaceted and complex. From navigating a fragmented regulatory landscape and identifying PFAS-free materials to managing the costs of compliance and staying updated with evolving regulations, medical device manufacturers must address numerous obstacles. By understanding these challenges and implementing effective strategies, manufacturers can better manage compliance efforts and minimize the impact on their operations and bottom line.
The impact of PFAS regulations in medical devices is multifaceted for the manufacturers, involving significant monetary costs, operational adjustments, and shifts in market dynamics. While the financial burden of compliance can be substantial, the long-term benefits of adhering to regulations—including enhanced market access, improved consumer trust, and alignment with sustainability goals—can outweigh the costs. Manufacturers that proactively address these challenges and invest in innovative solutions will be better positioned to navigate the evolving regulatory landscape and achieve lasting success.
Achieving PFAS compliance requires a strategic and proactive approach. By conducting thorough risk assessments, substituting PFAS-containing materials, optimizing processes, and implementing robust monitoring and reporting systems, medical device manufacturers can navigate the complex regulatory landscape effectively. Engaging with regulatory bodies and staying informed about industry trends will further support compliance efforts and ensure that manufacturers are well-prepared for the evolving PFAS regulatory environment.
Key Takeaways
- Regulatory Landscape: The global regulatory environment for PFAS is marked by stringent controls and evolving requirements. From international treaties like the Stockholm Convention to regional regulations such as the EU’s REACH and the U.S. EPA’s action plans, manufacturers must stay informed about diverse and often changing regulations. This comprehensive overview underscores the necessity of keeping abreast of both global and local regulations to ensure compliance.
- Impact on Medical Device Innovation: PFAS regulations can have significant implications for innovation in the medical device industry. While these regulations aim to protect public health and the environment, they also present challenges in terms of material selection and product design. Manufacturers need to be proactive in exploring alternative materials and processes to comply with restrictions and continue delivering innovative solutions.
- Strategies for Compliance: Achieving PFAS compliance involves a multi-faceted approach. Strategies include investing in research and development to identify and implement alternative substances, enhancing testing procedures to ensure compliance, and collaborating with industry stakeholders to share knowledge and best practices. By adopting these strategies, manufacturers can navigate the regulatory landscape more effectively and maintain their competitive edge.
- Addressing Common Challenges: Compliance with PFAS regulations often involves overcoming several hurdles, including understanding complex regulatory requirements, managing supply chain impacts, and addressing material safety concerns. Developing robust compliance programs, engaging with regulatory bodies, and leveraging technological advancements can help address these challenges effectively.
- Proactive Measures for the Future: As regulations evolve and new standards are introduced, it is crucial for manufacturers to adopt a proactive approach. This includes staying informed about regulatory changes, investing in continuous training for regulatory and compliance teams, and fostering a culture of safety and innovation within the organization.
Moving Forward
The journey toward PFAS compliance and regulation is ongoing, and medical device manufacturers must be prepared to adapt to new challenges and opportunities. By staying informed, embracing innovative approaches, and collaborating with industry peers, manufacturers can not only comply with current regulations but also position themselves as leaders in the industry’s response to PFAS challenges.
The insights provided in this guide are intended to equip manufacturers with the knowledge and tools needed to navigate the complexities of PFAS regulations. As the regulatory environment continues to evolve, maintaining a forward-thinking and adaptable approach will be key to achieving long-term success in the medical device industry.
For further reading, exploring related blogs on PFAS challenges, compliance, risks, restrictions, and testing can provide additional insights and practical advice. Each aspect of PFAS regulation intersects with the others, creating a comprehensive framework for managing these substances effectively.
By integrating these insights into their compliance strategies, medical device manufacturers can ensure that they are not only meeting regulatory requirements but also contributing to a safer and more sustainable future.
Partner with Tata Elxsi for Expert PFAS Compliance Solutions
As medical device manufacturers navigate the intricate landscape of PFAS regulations, having a knowledgeable and experienced partner can make all the difference. Tata Elxsi’s PFAS Compliance services offer comprehensive solutions to help your organization manage and mitigate PFAS-related risks effectively.
Tata Elxsi provides specialized expertise in PFAS regulatory compliance, offering a range of services designed to support medical device manufacturers in meeting stringent regulatory requirements. Our solutions are tailored to address the specific challenges of PFAS compliance, ensuring that your products not only adhere to current regulations but are also prepared for future changes.
Here’s how Tata Elxsi can assist you:
- Regulatory Strategy Development: We work with you to develop a robust regulatory strategy that aligns with both global and regional PFAS regulations. Our team helps you understand and navigate the complex regulatory landscape, providing clear guidance on compliance requirements and strategies.
- Material and Process Assessment: Our experts evaluate your materials and manufacturing processes to identify and mitigate PFAS-related risks. We assist in selecting alternative substances and modifying processes to ensure compliance with PFAS restrictions and bans.
- Testing and Analysis: Tata Elxsi offers comprehensive PFAS testing and analysis services to ensure that your products meet regulatory standards. Our state-of-the-art facilities and methodologies provide accurate and reliable results, helping you maintain compliance and address any potential issues proactively.
- Compliance Documentation: We help you prepare and maintain the necessary documentation for regulatory submissions and audits. Our services ensure that all required information is accurately documented and readily available, facilitating smoother regulatory interactions.
- Training and Support: We provide training and support to your team, equipping them with the knowledge and tools needed to manage PFAS compliance effectively. Our training programs cover regulatory requirements, best practices, and emerging trends in PFAS management.
At Tata Elxsi, we understand the critical importance of PFAS compliance in the medical device industry. Our goal is to partner with you to navigate these challenges successfully, ensuring that your products are safe, compliant, and innovative.
Discover how Tata Elxsi can support your PFAS compliance journey. Visit our PFAS Compliance Service Page to learn more about our services and how we can assist you in achieving regulatory success.
Contact us today to schedule a consultation and explore how our PFAS compliance solutions can benefit your organization.
Author: Dolly Sharma, Practice Lead