Attention
This website is best viewed in portrait mode.
Publication Name: Autocarpro.in
Date: August 05, 2024
From design to deployment: safety innovations in battery packs
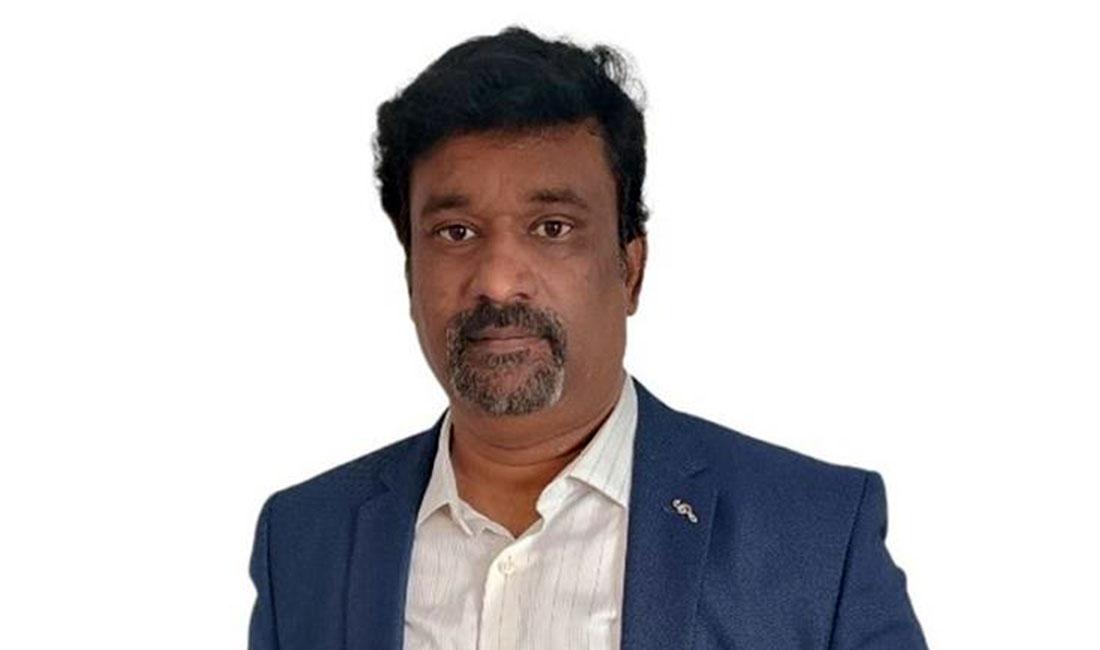
A robust battery management system integrates a Complex Device Driver (CDD) with strict functional safety requirements and advanced control algorithms to ensure safe and efficient battery operation.
The electric vehicle (EV) industry has been evolving rapidly in recent years, both in India and globally. A crucial element in the advancement of EVs is battery technology. For those unfamiliar, batteries are essentially compact, enclosed systems that supply power to electric vehicles. Modern batteries are now more energy-dense, offering numerous benefits and helping to tackle various challenges faced by the EV market.
Safeguarding Battery Pack Systems
The safety of battery packs is crucial to ensure that the EV runs smoothly for a long time. As the powerhouse of the electric vehicle, ensuring all components of the Battery Management System In simple terms, a BMS is a hardware system integrated with software that manages the battery pack for any anomaly happening and BTMS (Battery Thermal Management System) run and operates smoothly is essential.
Unfortunately, EVs have experienced several accidents, often due to overheating, which can lead to fires or short circuits. A well-structured and well-designed BMS will continuously monitor each cell within the battery pack for temperature and aging. Here are a few key factors to consider when discussing the safety of battery packs.
Battery Thermal Management Systems (BTMS)
Alongside BMS, there is also TMS which extends to the Thermal Management System. As the name suggests, the TMS maintains the EV’s temperature at the right level. This system helps prevent overheating, which can lead to thermal runaway, a condition where a battery cell enters an uncontrollable self-heating state. A typical battery pack requires a temperature range between 25°C to 40°C and the delta temperature between the cells or modules should not exceed 5°C. There are a few considerations in designing and packaging a battery pack to attain these criteria.
Firstly, the packaging consideration differs between various form factors such as cylindrical cells can be packaged with an optimum cell gap which can achieve good temperature control in terms of conduction and convection of cells. On the other hand, prismatic cells with high energy density can generate more heat and thus, require Thermal insulation materials and adhesives.
Effective thermal management not only promotes the longevity of the battery pack but also enhances its safety. Additionally, NTC thermistor temperature sensors are critical components for Li-Ion battery charging and safety. They give essential temperature data required to maintain the Li-Ion battery's optimal state during the charging cycle. Temperature control during charging extends battery life and protects against the risks associated with Li-Ion batteries.
Fire Suppression Systems
Incorporating a fire suspension system within the battery pack helps to quickly extinguish any fires that may start due to a cell failure. In addition, the selection of fire suppression system type plays a major role, whether it is a condensed aerosol generator-based or tube- based extinguishing system plays a vital role. The parameters such as space, weight, activation and operating temperatures, pressure, and certified lifetime also are important aspects in the selection.
These systems are typically structured with fire-resistant materials. EVs also use integrated fire suppression chemicals such as Potassium carbonate suspended in a blend of inert gases as part of the fire suppression system.
Pack Design
More importantly, design plays a crucial role in ensuring the safety of the battery pack in EVs. For instance, Lithium-ion battery cells are designed with safety features like thermal shutdown mechanisms and separators to prevent internal short circuits and thermal propagation.
Further, structural design is also extremely important for the safety of battery packs. Generally, battery packs are housed within robust enclosures with crash-resistant structures to protect against physical damage from collisions and impacts.
Software Systems
Software systems are essential to ensure seamless communication between the battery pack and other vehicle systems, such as the powertrain, charging system, and driver interface.
For instance, Application Software and Basic Software ensure all systems are synchronised to transmit safety-critical data and battery status enabling appropriate responses in case of issues. A robust battery management system integrates a Complex Device Driver (CDD) with strict functional safety requirements and advanced control algorithms to ensure safe and efficient battery operation.
Designing Safety Innovations of BMS
While ensuring all functional blocks of a BMS operate in sync, it is crucial to prioritise safety in its design. It’s well agreed upon that the design plays a crucial role where the safety of BMS is considered.
For instance, every battery pack contains electrical cells, and the design dictates not only the battery's safety but also how these cells are managed. A robust design is essential for controlling the battery management system and managing electrical current production within the EV.
While speaking of the design, it is important to note that EV batteries are relatively large and typically extend across the entire underfloor. As expensive components of the EV, they also add to the weight of the vehicle. It is imperative to minimize the weight of battery packs and ensure proper structural integration.
These elements ensure it seamlessly integrates with the vehicle’s frame, enhancing crashworthiness. In the event of a crash, the integrated design ensures the structure can absorb the load from mechanical impacts, shocks, or any crash incidents. In addition to structural design, fire suppression systems are also important aspects of BMS design. These systems are mandatory in EVs, particularly within battery packs, to swiftly extinguish any fires that might arise from cell failures.
Meeting Standards with Regulatory Compliance and Testing
Every component of a vehicle must undergo rigorous testing, and this is especially critical for EVs, where the battery pack system undergoes testing and qualification at every stage of development.
All BMS units need to adhere to stringent international safety standards and undergo extensive testing, including mechanical shock, vibration, thermal cycling, and electrical abuse tests. Compliance with these regulations ensures that the battery packs are safe under a wide range of conditions and scenarios.
Apart from industry standards, OEMs must also adhere to geography-specific regulations. For instance, there are various standards like AIS 048, ECE R100, UN 38.3, or ISO 26262 are crucial benchmarks. It is also essential for OEMs and service providers to understand each compliance for functional safety standards.
In conclusion, ensuring the safety of battery pack systems is crucial for advancing and gaining acceptance of electric vehicles. Manufacturers achieve this through meticulous design, robust structural integration, and adherence to stringent regulatory standards, ensuring these systems are both reliable and secure. Safety innovations play a key role, and a well-structured BMS design is vital for the longevity of electric vehicles.
Author: Perumal AT is the Head of Electrification CoE, EV/FCV – Mechanical and electromechanical Design. Views expressed are his own.