Attention
This website is best viewed in portrait mode.
Publication Name: Manufacturingtodayindia.com
Date: December 09, 2024
Revolutionising manufacturing with AI: From production efficiency to industry 4.0 transformation
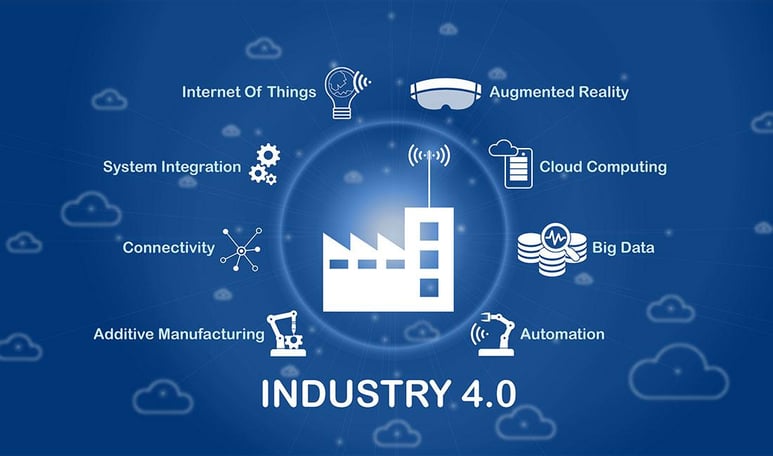
Explore AI’s role in improving manufacturing efficiency, safety, quality, and predictive maintenance.
Imagine a factory floor where machines predict their own maintenance needs, quality checks are instantaneous, and safety incidents are a thing of the past. This is not the future—it’s the reality AI is shaping today in manufacturing.
In the rapidly advancing world of manufacturing, the adoption of Artificial Intelligence (AI) has transitioned from being a futuristic concept to a pressing necessity. By leveraging AI, companies are achieving unparalleled levels of production efficiency, enhancing quality, and significantly reducing operational costs. The integration of AI-driven solutions with smart manufacturing and industry 4.0 is not merely about automation; it is about reshaping the very fabric of manufacturing processes to build smarter, interconnected, and more sustainable systems. The transformative impact of AI on smart manufacturing and industry 4.0 frameworks focuses on key applications in safety monitoring, quality control, predictive and preventive maintenance, supply chain and process optimisation.
Ensuring safety compliance: AI use cases and applications
Safety is a fundamental pillar of manufacturing. With stringent compliance requirements and the need for a secure working environment, manufacturers are increasingly relying on AI-driven tools to ensure safety compliance and mitigate risks. AI-powered surveillance systems monitor the workplace in real-time, identifying unsafe conditions or practices such as improper use of safety equipment or hazardous activities. These systems enable instant corrective actions, minimising accidents before they escalate.
Another key application of AI in safety is virtual access control. AI-powered secure zones restrict unauthorised entry into sensitive areas, significantly reducing risks associated with human errors or malicious activities. By embedding AI into safety protocols, manufacturers not only comply with regulations but also enhance employee welfare, creating a safer and more productive work environment.
Enhancing quality with intelligent monitoring
AI has revolutionised the realm of quality control, moving manufacturers from reactive to proactive quality management. Traditional quality checks often rely on human intervention, which is prone to errors and inefficiencies. AI, on the other hand, offers precision, speed, and consistency. AI-driven cameras and sensors can identify manufacturing defects such as missing components, incorrect assembly, or dimensional inaccuracies in real-time. These tools enable manufacturers to rectify issues immediately, minimising wastage and rework.
Predictive quality analysis, another game-changer, utilises machine learning models to forecast potential defects based on historical data. By predicting problems before they occur, manufacturers can implement preemptive measures, ensuring products meet customer expectations without compromise. This approach not only reduces waste but also strengthens customer trust in the brand.
Predictive maintenance: Eliminating downtime
Unplanned equipment failures are one of the most significant disruptions to manufacturing efficiency. Traditional maintenance strategies, often based on fixed schedules, fail to address the dynamic nature of machinery wear and tear. AI offers a smarter alternative: predictive maintenance.
Machine learning algorithms analyse data from sensors and historical records to predict when a machine is likely to fail. This predictive capability allows maintenance activities to be scheduled during non-peak hours, minimising disruptions to production. Additionally, AI provides insights into wear and tear patterns, enabling manufacturers to optimise maintenance schedules. By addressing potential issues early, companies can reduce downtime, extend equipment lifespan, and significantly lower maintenance costs.
Process optimisation: The efficiency multiplier
AI’s role in manufacturing goes beyond individual components; it extends to streamlining the entire production process. The key to sustained efficiency lies in continuous process improvement, a goal that AI tools are uniquely equipped to achieve. AI-powered time-motion studies analyse worker and machine movements to identify inefficiencies and recommend refinements. This data-driven approach ensures that resources are utilised optimally.
Real-time monitoring systems powered by AI offer continuous updates on production performance. Managers can use these insights to make informed decisions, addressing bottlenecks and reallocating resources swiftly. These capabilities foster a culture of continuous improvement, where AI serves as a catalyst for innovation and operational excellence.
Overcoming challenges: Unlocking AI’s full potential
Despite its transformative potential, AI adoption in manufacturing comes with its share of challenges, including data privacy concerns, integration complexities, and the need for workforce reskilling. Ensuring the secure handling of sensitive manufacturing data requires robust cybersecurity measures to mitigate risks and build trust. Integration hurdles can be overcome by collaborating with experienced AI solution providers, who can streamline the incorporation of AI tools into existing systems. Additionally, reskilling the workforce is crucial to fostering collaboration and enhancing productivity, as employees learn to work alongside AI technologies. By addressing these challenges with a strategic approach, manufacturers can unlock the full potential of AI and secure its long-term benefits.
The future of in manufacturing: embracing AI for a competitive edge
The role of AI in manufacturing is poised to expand further, encompassing innovations in robotics, supply chain optimisation, and personalised customer experiences. As technologies like edge computing and 5G mature, the synergy between AI and manufacturing will drive unprecedented levels of efficiency and innovation.
However, the journey doesn’t end with technological adoption. To fully realise AI’s potential, manufacturers must embrace a mindset of continuous learning and adaptation. This involves fostering partnerships, investing in R&D, and cultivating a culture that values data-driven decision-making. AI is not just a tool; it is a strategic enabler that empowers manufacturers to achieve operational excellence. By integrating AI into safety protocols, quality management, maintenance, and process optimisation, companies can create a holistic approach to production efficiency.
The time to act is now. Manufacturers that embrace AI today will not only gain a competitive edge but also lay the foundation for a sustainable, innovative, and customer-centric future. In an era where change is the only constant, AI stands as a beacon of opportunity, guiding manufacturing into a new age of possibilities.
Author: Anup S S, Practice Head, Artificial Intelligence, Tata Elxsi