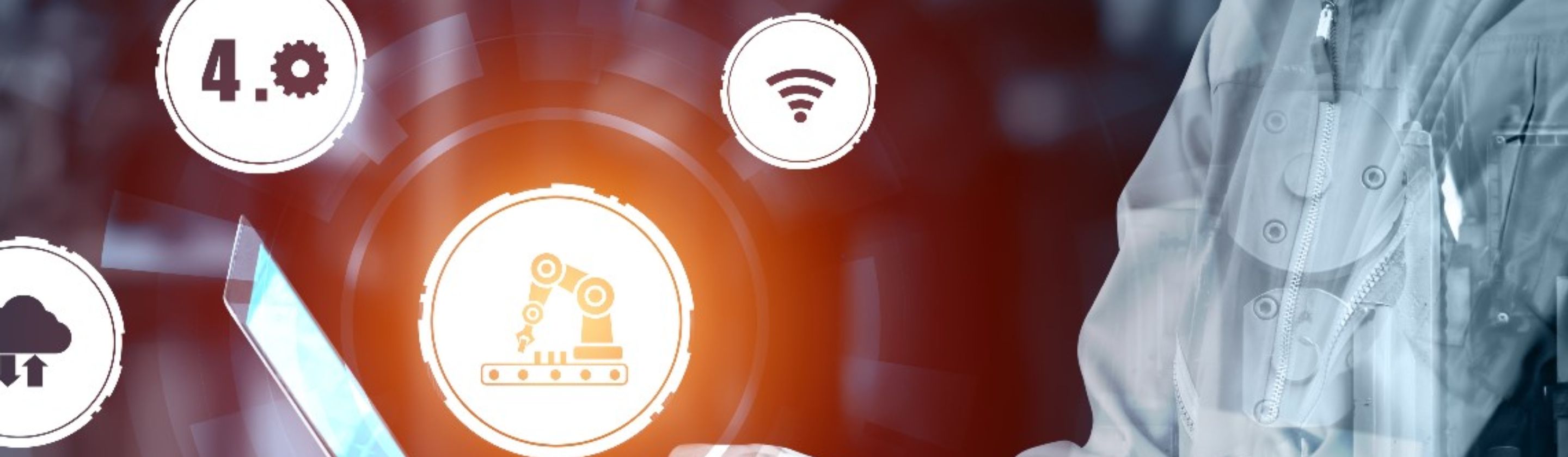
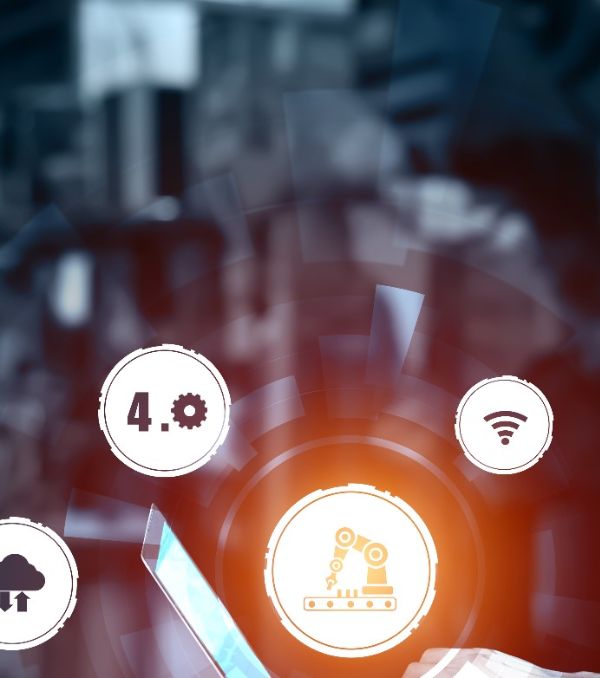
Industry 4.0 and the Future of Manufacturing
Explore Tata Elxsi’s insights on Industry 4.0 and the future of manufacturing—uncovering the use of AI, IoT, and automation in enabling intelligent, connected factories.
Read Whitepaper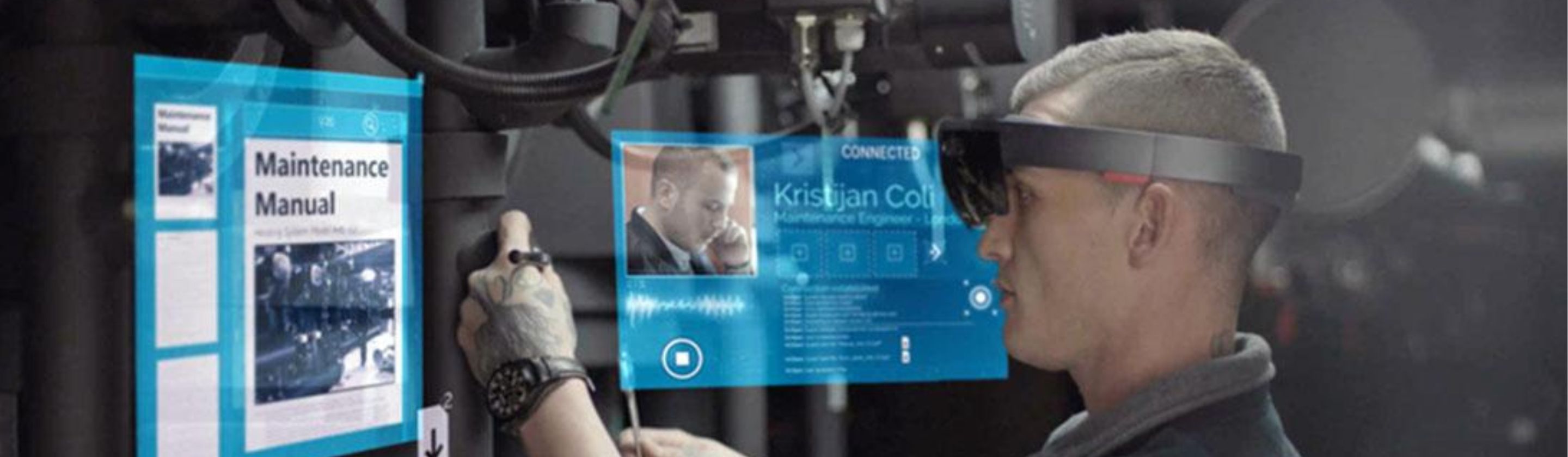
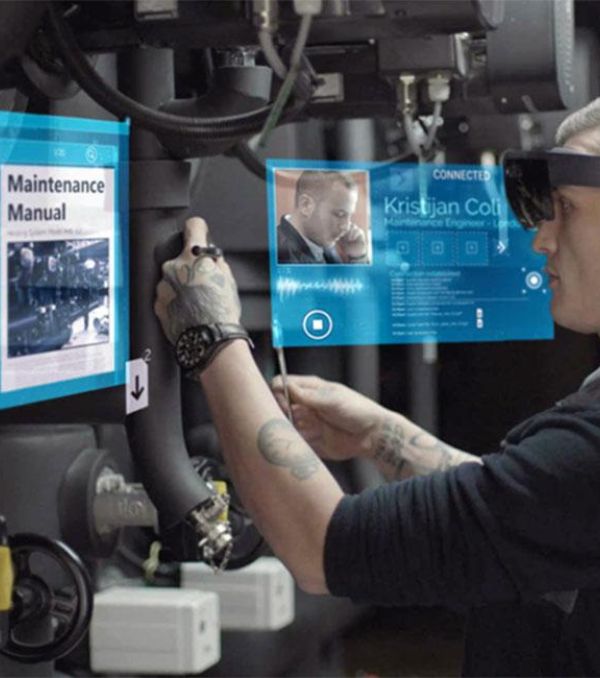
Tata Elxsi and Lenovo
Tata Elxsi and Lenovo join forces to deliver scalable, immersive XR solutions for enterprises—enabling easy deployment and enhanced digital transformation through AR, VR, and MR technologies.
Read MoreIndustry 4.0 is bringing the physical and virtual worlds together
The manufacturing industry is rapidly evolving with the advent of Industry 4.0, characterized by the convergence of digital technologies, smart automation, and data-driven intelligence. Tata Elxsi empowers organizations to embrace this transformation by delivering integrated solutions across digital manufacturing, AI/ML-driven analytics, IoT connectivity, and AR/VR-powered training.
With deep domain expertise and scalable frameworks, we enable enterprises to enhance operational efficiency, productivity, and worker safety. Our approach bridges the physical and digital worlds through Digital Twin, predictive maintenance, and intelligent automation, aligning technology investments with business goals. From factory floor to cloud, we accelerate your journey to smart manufacturing.
Building AI-Driven Sustainable Automation for Steel Industry
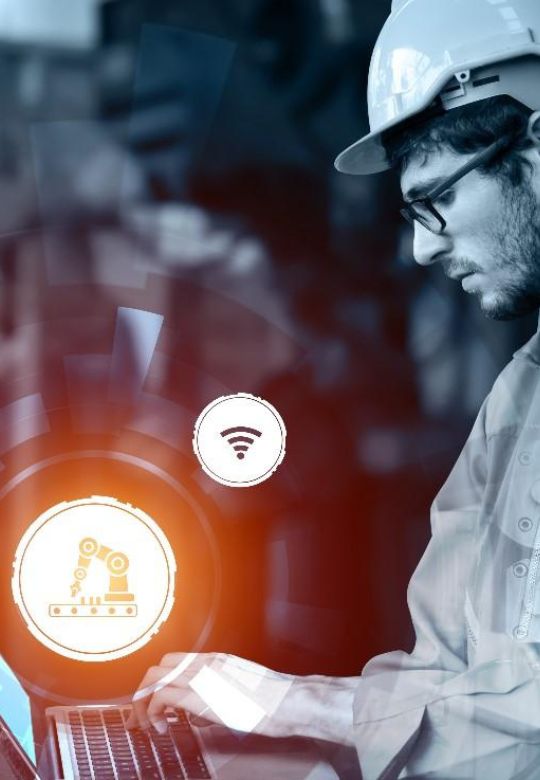
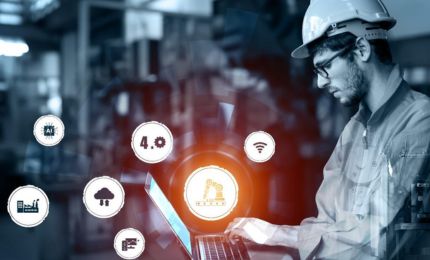
Implementing Industry 4.0: Challenges
Smart factories will open up new possibilities such as predictive maintenance, improved worker safety, and quality control. Shop floor connectivity will lead to stronger integration with ERP for better demand forecasting and resource allocation. We will see significant results like production optimization and operational efficiency improvement. Proper smart factory implementation will lead to agility, speed to market, and highly flexible lines.
To fully reap the benefits of Industry 4.0, organisations must overcome the challenges of implementing large-scale smart manufacturing solutions. The current workforce's lack of technical skills is a major impediment to smart factory deployment. If the organisation wants to scale beyond pilot projects, it must bring a diverse set of capabilities to the team. This will include expertise in solution development to testing, deployment, and maintenance.
The separation of protocols, components, products, and systems is another significant challenge. This lack of interoperability limits the options for upgrading system components and switching from one vendor to another.
Industry 4.0 Solution Framework
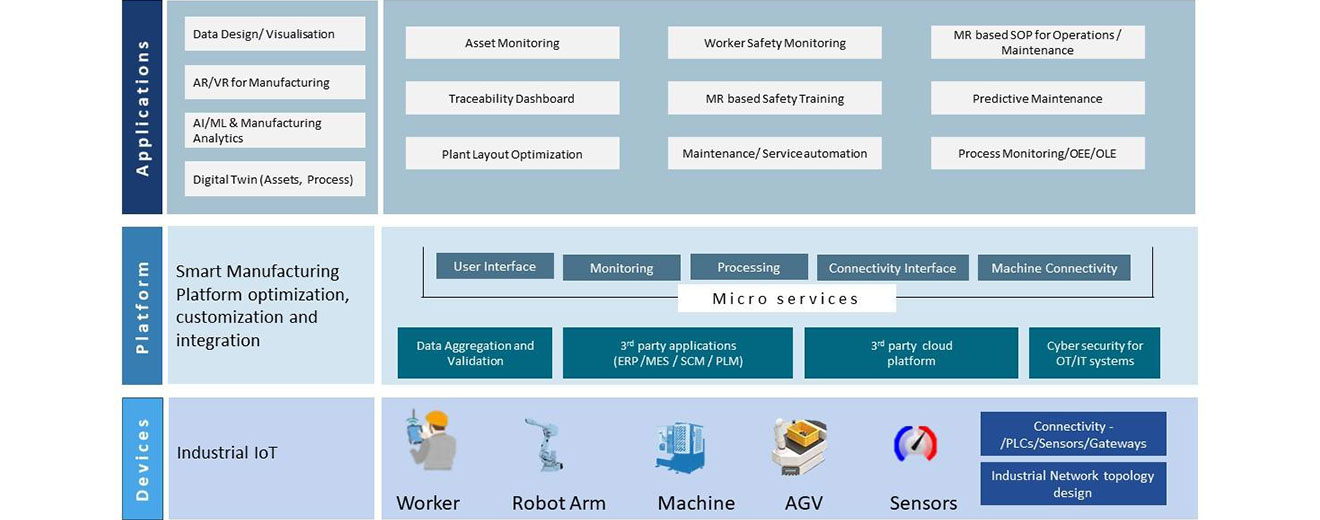
Process analysis & optimization
- Overall equipment efficiency (OEE) optimization
- Overall line efficiency
- Control & monitoring
- Knowledge automation
- Autonomous navigation and automated guided vehicle development
Factory Automation
- Industrial gateways
- Data lake creation and management on-premise and on cloud
- Automated guided vehicles
- Predictive analytics and maintenance
- Plant performance analytics
- AI-based video analytics
Design & visualization
- Plant simulation
- Digital twin
- Generative design
- 3D modelling
- AR / VR / MR applications for operational & maintenance SOPS
Why Tata Elxsi?
- Functionality-rich accelerators for offering flexible and scalable solutions
- COEs for IoT, AI, and Extended Reality
- Partnerships with I4.0 Ecosystem (Automation and Sensors / Device OEMs & Industrial ISVs)