Attention
This website is best viewed in portrait mode.
-
industries
- automotive
- vehicle systems engineering
-
Body Design and Engineering
Body Design and Engineering
Scale | Engineer | Enhance
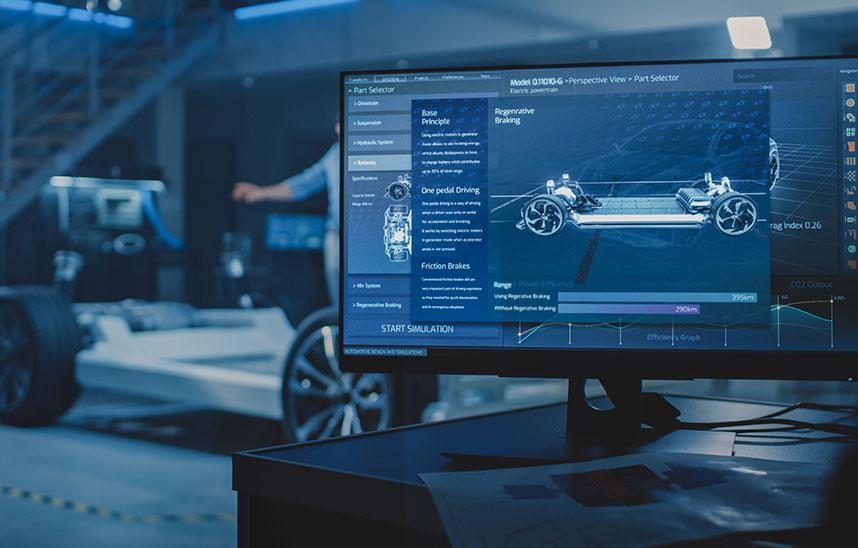
Body Design and Engineering
Scale | Engineer | Enhance
Designing the Cars of Tomorrow
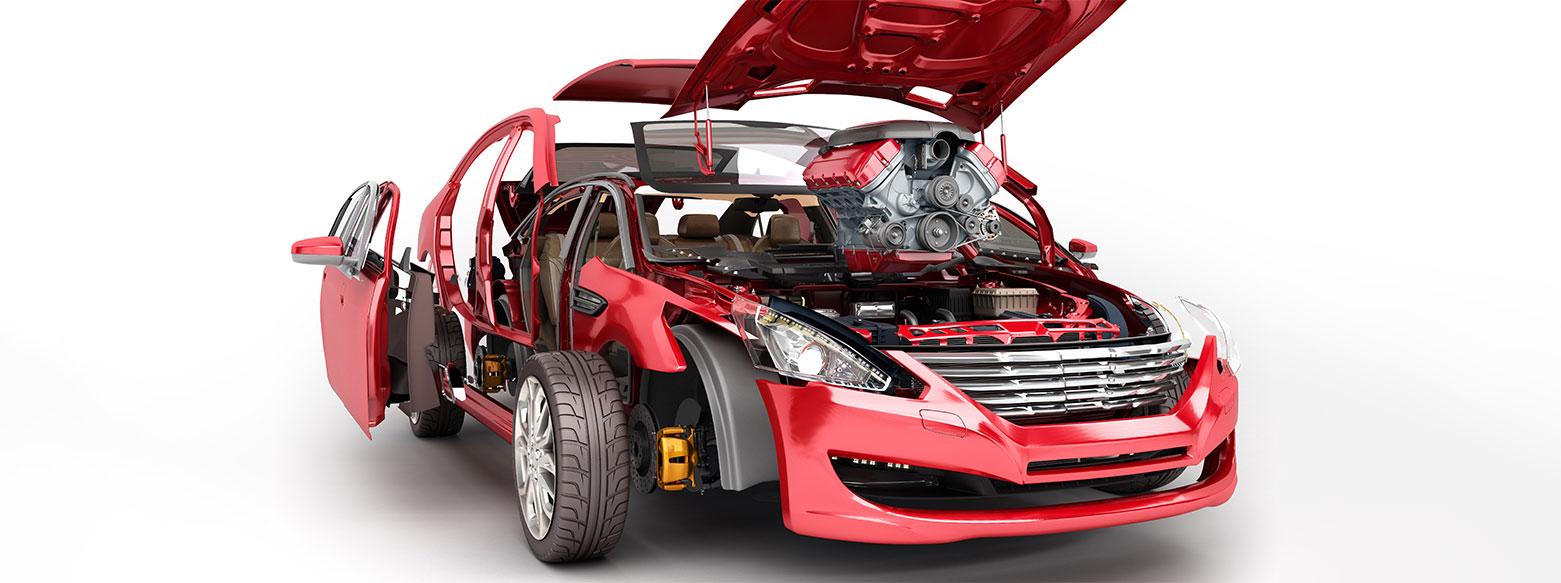
Automakers are constantly striving towards improving performance and efficiency through lightweighting, and aerodynamic body designs. This is especially true in the case of Electric Vehicles where body weight has a direct impact on battery performance.
Shorter product development cycles, the need to reduce costs of designing, testing, and producing scalable solutions is pushing automotive OEMs to develop modular body designs.
Automotive OEMs today prefer a turnkey design and engineering partner to help them address the complete ecosystem requirements.
Tata Elxsi provides unified design and engineering expertise that spans across:
- Styling and Surfacing
- Engineering Design and Development
- Post Development Support
- Verification and Validation
- Manufacturing Engineering
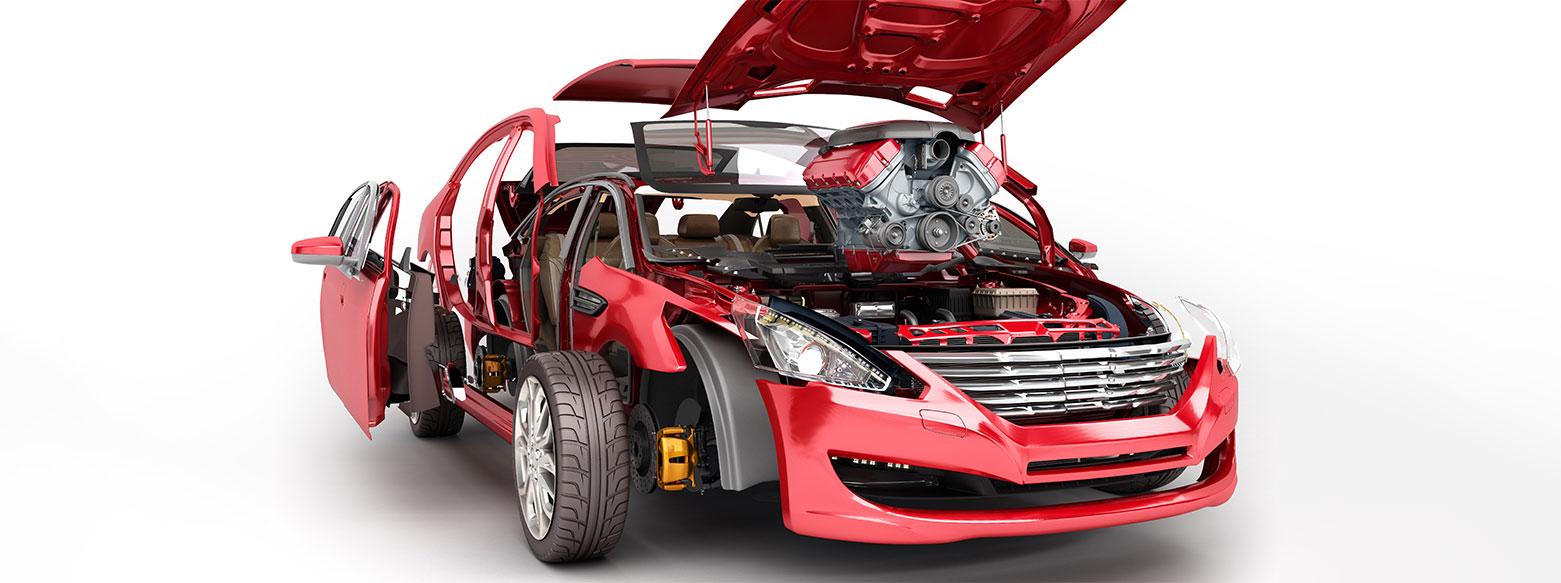
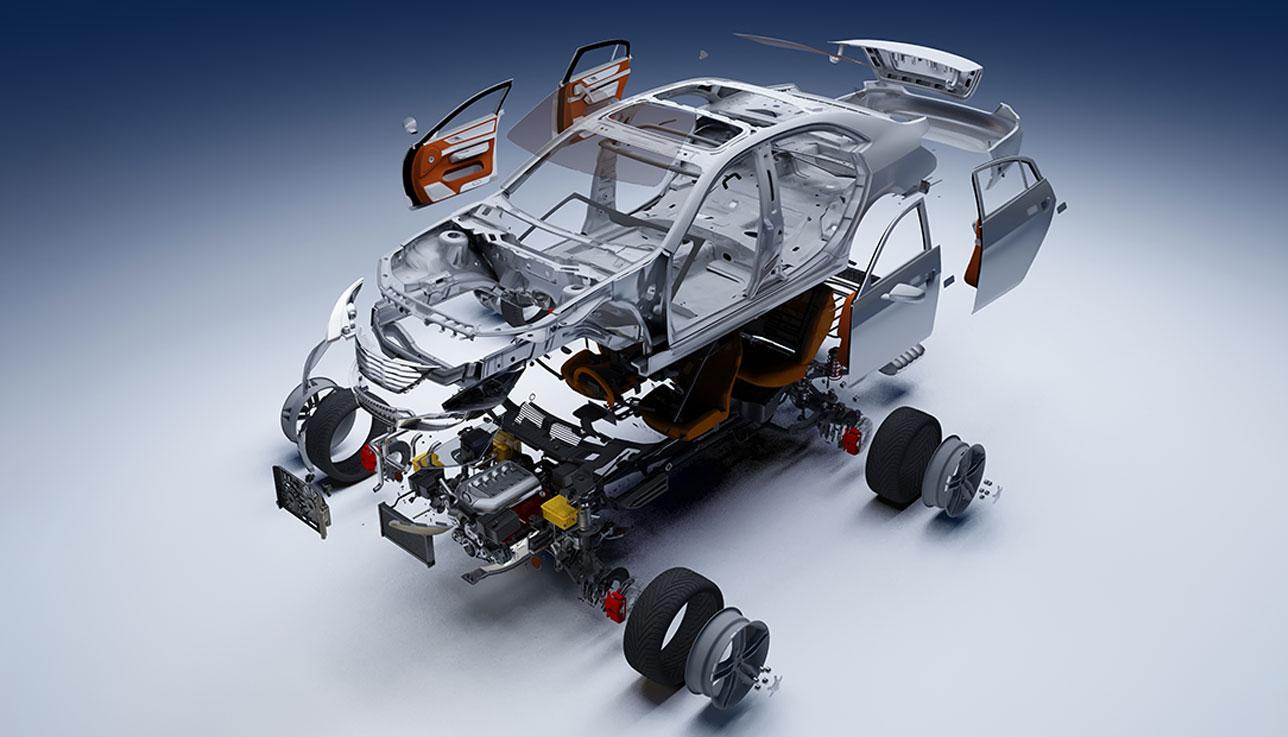
Here’s How We Can Help You
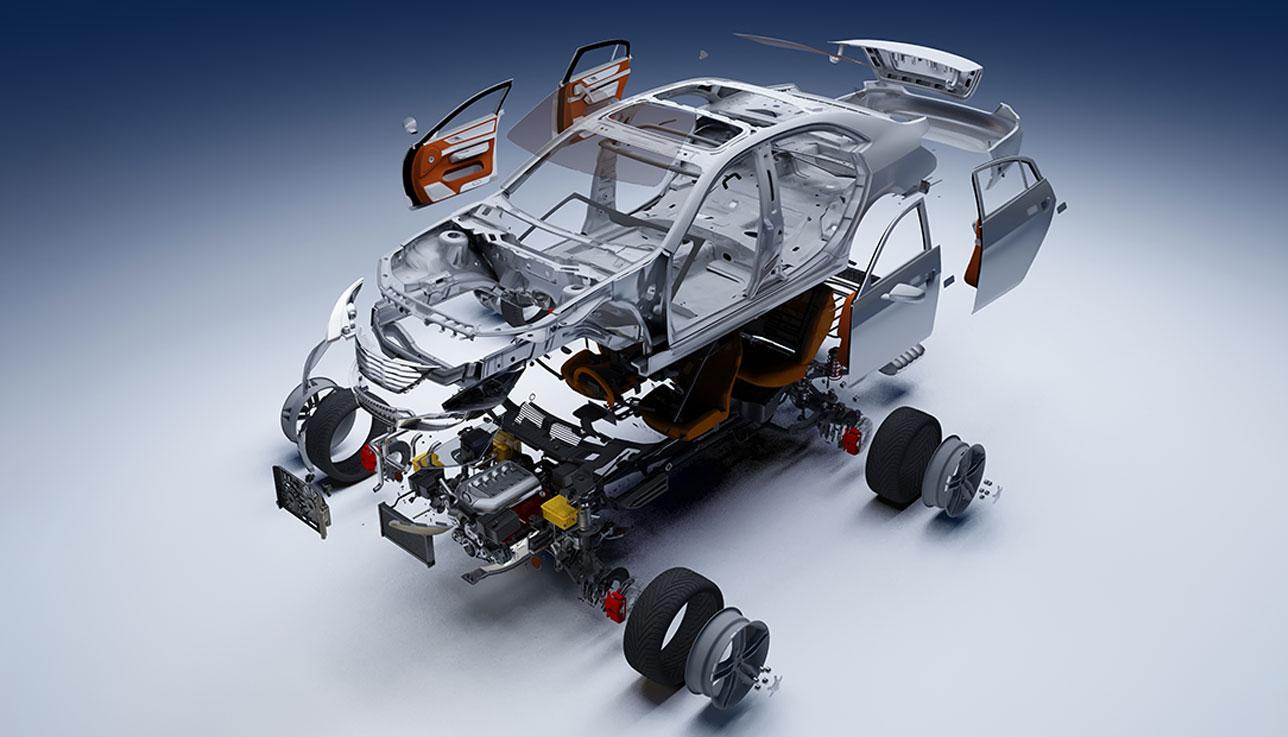
Modular Design Expertise
- Expertise in developing Modular Chassis and Car bodies across segments for varied powertrain
Research and Design
- Lightweighting to meet regulations and maximize efficiency to address CASE requirements
- Dedicated VAVE teams to support at a system and commodity level
- Data-driven insights to help make more informed decision-making from multiple CAE simulations
Future Ready Sustainable solutions
- Advanced Manufacturing Engineering expertise for new material and process deployment
Service Framework
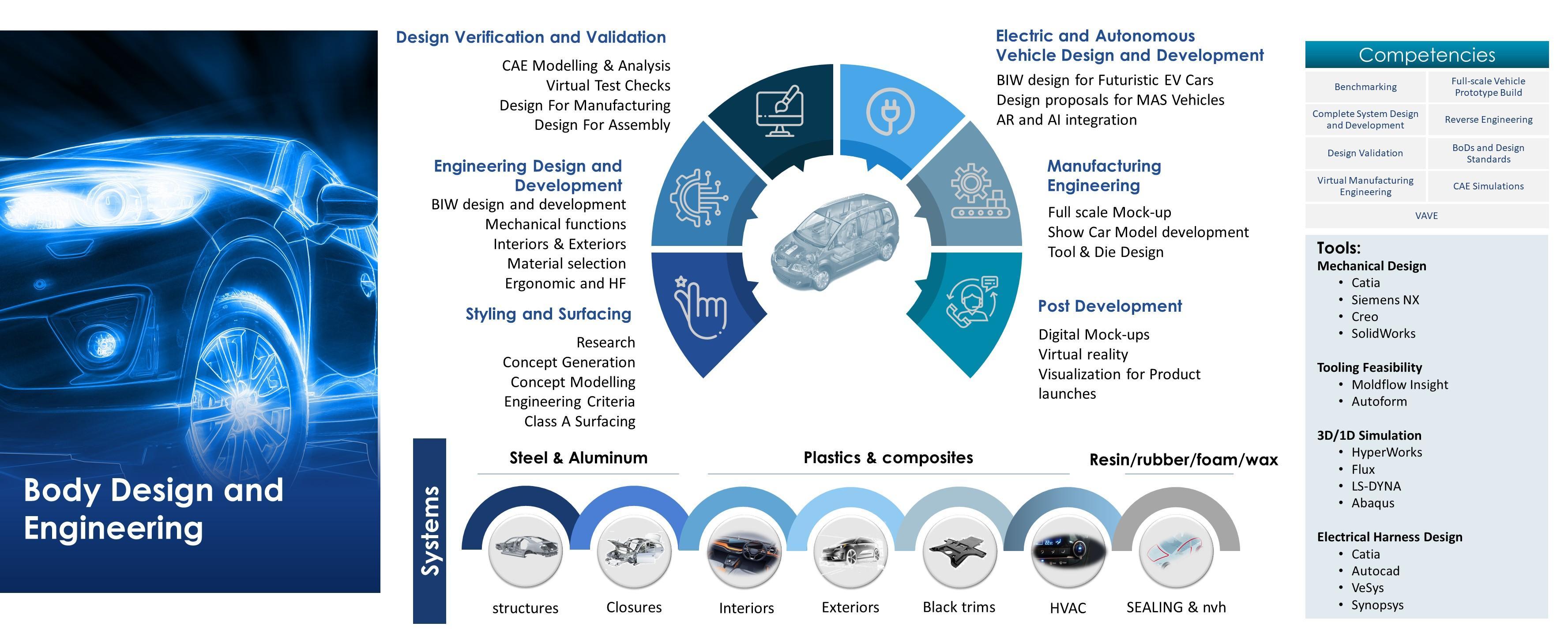
Why Tata Elxsi?
- Comprehensive global network for body-chassis engineering
- Leading in material science, metallurgy, advanced manufacturing techniques, and sustainable innovation
- Design efficiency through simulation, notably saving time, effort, costs, and materials
Subscribe
To subscribe to the latest updates & newsletter